At nearly every commercial airport around the world, there is a necessity for ground vehicles to move luggage and cargo around. At airports without large aircraft stands – the vast majority of airports around the world – there also arises a necessity for vehicles to “push back” aircraft out of their gates and onto the taxiway so that they may get going on their journeys. What kind of vehicle can combine these two necessary functions? Enter the world of airport tractors.

Barcex via Wikimedia
A brief history of the airport tractor
In the early 1900s, most American pilots were known to be daredevils who would “buzz” small American farm towns by flying extremely low over the roofs of homes and obstacles as a form of entertainment for the locals. Once pilots were done with their “buzzing” shenanigans, they needed a place to land which, in the 1910s and 20s, was any place that was an open field. Most of the time, the fields pilots landed in were owned by farmers.
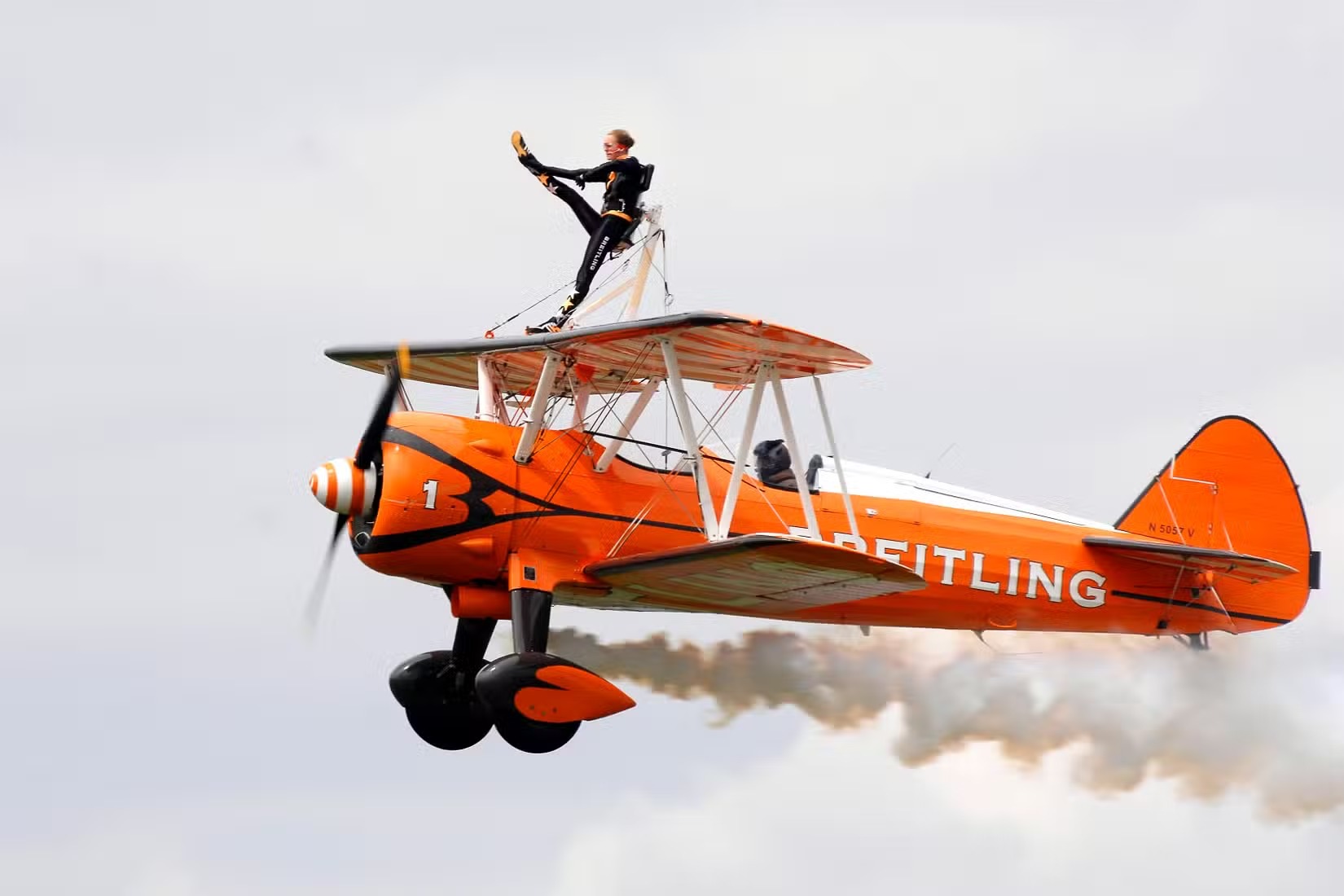
Photo: Tech. Sgt. Lee Osberry, U.S. Air Force, Wikimedia Commons
When a daredevil pilot landed their plane on a field owned by a farmer, they would often cut deals with the farmer. Most of the time, these deals would involve the daredevil pilot performing stunts for an audience of people and stunt performers doing tricks while the pilot flew their plane. Farmers would typically help out their new business partners by using their tractors to tow the pilot’s plane across their rough fields. Hence, the name “tractor” that we use today to refer to the ground service equipment (GSE) vehicle that pushes or pulls planes at airports.
In 1923, Clark Tructractor Co. began to manufacture a tractor meant to pull heavy freight and industrial loads. This tractor became the basis for most future airport tractor designs. Tractors such as the one manufactured by Clark Tructractor Co. began to rumble onto airports as early as the 1930s to deliver passenger luggage as commercial air travel grew in popularity.
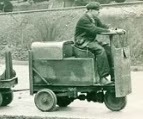
Photo: eagletugs.com
After World War 2 (the late 1940s into the late 1950s), air travel began to boom across the world, and it was during this time that the first vestiges of the GSE industry began to flourish. GSE manufacturers began to develop the necessary equipment such as ground auxiliary power units (APUs), and dedicated airport tractors to help keep up with this boom.
In the late 1950s, a French company (now known as TLD), debuted the Tracma to replace the agriculture-oriented tractors previously used at airports around the world. This model of tractor all but revolutionized airport GSE, as it was designed and manufactured for use solely at airports.
Unlike its predecessors, the Tracma featured an all-wheel drive option, which would prove useful when pushing and pulling larger aircraft as well as heavy cargo loads. This tractor was small and powerful. Soon enough, its design became a staple of GSE vehicle design.
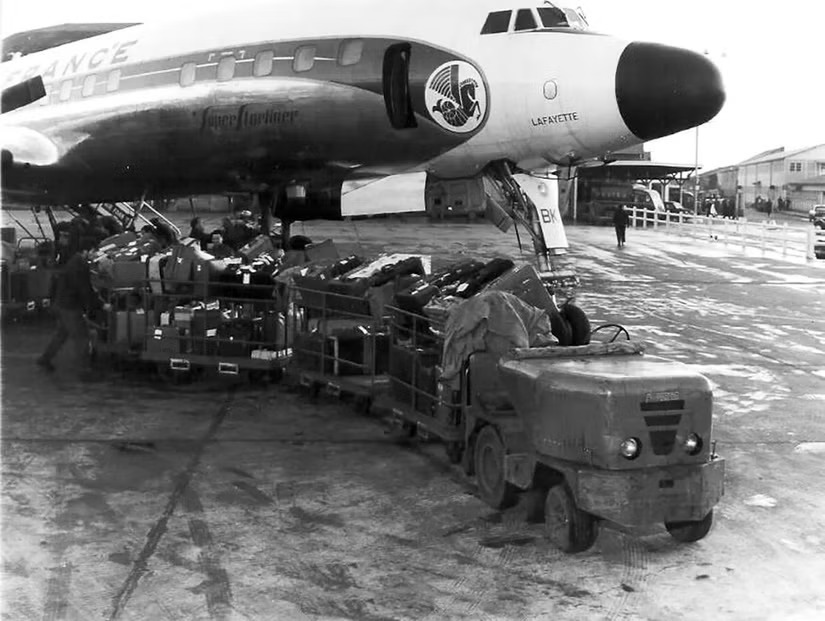
Photo: aviationpros.com | TLD Group
The way the Tracma and most airport tractors prior to it were able to push and pull aircraft was with a tow-bar. The tow-bar used during push-back would be hitched to an airport tractor. The opposite end of the tow-bar would be hitched to the wheel of the aircraft the tractor was pushing back. Beginning in the late 1940s, tractors also began to be used for the purpose of transporting cargo and luggage around airports.
The Tracma, and designs like it that were powered by diesel fuel, would become the standard for airport ground operations for the next 40 years up until the early 2010s, when electric tractor designs would begin to emerge.

Modern Airport Tractors
Around the world, airport tractors are commonly referred to with the word ” aircraft tug“, which is the more common and used name for the vehicle. In 2024, there exists two primary categories of airport tractors – conventional and towbarless – both of which have their own advantages and disadvantages.
Conventional tractors are those that utilize tow-bars for aircraft push-back and towing operations. These types of tractors are ideal for airports looking to spend less on maintenance and inspections. However, conventional tractors can only be used at airports that see fewer aircraft types, typically smaller short to medium haul aircraft. This is due to the relatively limited engine power that these tractors have. Even new, small conventional electric tractors struggle to push back larger aircraft.
Unlike their towbarless counterparts, conventional tractors can be utilized in their downtime when not handling aircraft. At airports around the world, it’s a common practice for airport baggage workers to use conventional tractors to haul cargo and luggage from aircraft to airport facilities.

Photo: Denver International Airport
On the other hand, towbarless tractors are popular and primarily seen at large international airports like Frankfurt (FRA) or John F. Kennedy International Airport (JFK) due to their ability to pull heavier aircraft (including 747s and A380s), better visibility when towing due to their flat designs, and better brakes for pulling larger aircraft.
As both types of tugs are (often times) required to push and pull multiple tons of weight at once, most tractors are equipped with all-wheel drive. When combined with the use of diesel and gasoline in older tractors, this leads to increased noise and environmental pollution.
As climate change is pushing the aviation industry towards a more sustainable future, manufacturers of airport GSE and tractors are being forced to innovate to keep up with the times.

Photo: Malaysia Airlines
GSE manufacturers have been doing this via the pursuit and manufacturing of electric battery-powered tractors and service vehicles. In 2024, most major GSE companies offer an electric option for both conventional and towbarless tugs (that are based on an airport’s needs and preferences).
Electric tractors in their various forms are easier for airports to maintain due to their (relative) lack of moving parts when compared to their fossil-fuel powered counterparts. On top of this, electric tractors can provide the same amount of power in less time due to their electric motors and higher efficiency in converting battery power into the mechanical power needed to push and pull aircraft. A benefit for airport employees in operating electric tractors is the lessened noise that comes from quieter e-motors and no emissions. The only real downside to the use of electric tractors is that they’re typically more expensive than their diesel or gasoline counterparts, because of the extra cost that gets factored in when sourcing the materials needed for electric tractor batteries. Although this is a common problem seen in the electric car industry as well.
Besides their primary function, fossil fuel and battery-powered tractors are used in hauling cargo crates around airports. Those little vehicles with three or four crates in tow that you see driving away from your aircraft are indeed tractors, and believe it or not, these tractors may be self-driving in the future.
Similar to how companies are training autonomous vehicles (coloquially known as “robot-taxis”) on the streets of San Francisco California, some airports around the world such as Cincinnati/Northern Kentucky International Airport (CVG), have been testing vehicles called “Auto-Dolly Tugs”, electric self-driving tractors designed by GSE company Aurrigo.
Auto-Dolly Tugs are meant to transport cargo containers between aircraft and the main terminal at CVG airport. Aurrigo’s Auto Dolly Tugs are equipped with “robotic arms” that enable these self-driving autonomous vehicles to load and offload cargo containers.
While each Auto-Dolly can only carry one cargo container, up to three can be hooked together to carry multiple containers in a “train”, similar to how human-operated tractors transport cargo today.
Aurrigo’s tractors are able to drive autonomously around airports, because they use a map overlay of the airport and GPS tracking data to precisely locate where the autonomous tug is at all times. Singapore Changi Airport (SIN) is testing the same technology with Aurrigo as well.
New technology aside, how much do airport tractors cost?
Most airport tractors used for the handling of large commercial airliners can cost airports upwards of $500,000 just one or two tractors.
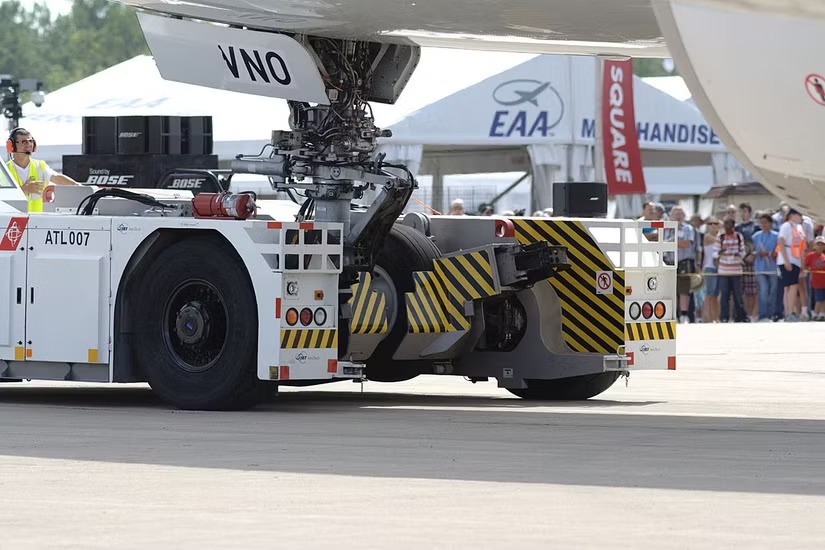
Photo: Michael Pereckas | Wikimedia Commons
Smaller mixed use tractors (that can be used for aircraft ground operations and baggage handling) run anywhere from $50,000 to $150,000 used, with older diesel models costing $20,000-$50,000.
Large push-back tractors seen at major international airports can cost airlines up to $600,000 depending on the type and engine configuration.
The number and type of tractors needed at an airport depends on the operations going on at that particular airport. Take Aspen Airport (ASE) in Colorado, USA. A small airport like Aspen will need only require around 10 to 20 small diesel or electric-powered tractors to maintain its ground operations.
Meanwhile, a large international airport like Newark Liberty International Airport(EWR) will need hundreds of conventional and towbarless tugs in order to keep its varied ground operations from cargo to short, long haul and private flights running smoothly.
At the end of the day, tractors are what keep airports moving. They allow aircraft to utilize jet-bridges and gates, as well as facilitate the transport of luggage and cargo around airports. Without tractors, modern commercial aviation would not be able to flourish in the way it continues to do so today.
Source: Simple Flying
Warning: Illegal string offset 'cookies' in /home/u623323914/domains/eng.bayviet.com.vn/public_html/wp-includes/comment-template.php on line 2564